With the development and progress of socialized production, the professional division of labor and machinery is becoming more and more refined, and the matching and connection of various professional equipment has made the entire logistics system operate in an orderly manner, and the efficiency has been doubled.
In the traditional storage system, because there are no more options, all handling, stacking, loading and unloading may be completely solved by a forklift, which is manifested in the warehouse, which shows a large area, low space utilization, and many people. , The goods are piled up in a scattered way, the shipment is slow, and the vehicles are queuing in the peak period.
Today, a complete set of processes from warehousing, putting on the shelves, picking, distributing to leaving the warehouse can be carried out by counterbalanced forklifts, various indoor handling machinery or automated unmanned handling equipment, conveyor belts, automatic sorting equipment, etc. Many kinds of professional equipment are segmented, and the instructions and connections can be completed through electronic forms or wireless transmission between various equipment.
A warehouse environment that is as bright, clean, fast, efficient, and orderly as an office is readily available.
Since the invention and use of pallets and the beginning of container handling, forklifts (including indoor and outdoor forklifts) have become the main tool for material handling. For a long period of time in the future, forklifts with innovative functions and higher and higher degrees of automation will continue to be realized. It will also remain dominant in the handling field.
In the following, we will discuss how to choose the appropriate forklift according to the environment and some factors that need to be considered in the selection of forklift.
1. First, let's take a look at the classification of forklifts
According to the use environment of the forklift, it can usually be divided into two categories: indoor use and outdoor use. Outdoor forklifts are usually large-tonnage diesel, gasoline or liquefied gas forklifts, such as container forklifts and cranes used in docks or container transfer stations. Indoor forklifts are basically battery trucks.
Now the world's major forklift manufacturers can provide hundreds of specifications of products, we usually divide these different specifications into several series, and their main products can be roughly divided into 8 series:
● Hand Pallet Trucks
● Power Pallet Trucks
● Support Arm Stacker can be divided into three types: self-propelled, standing and riding
● Electric Counterbalance Truck
● Diesel/LPG Counterbalance Truck
● High Rack Stacker
● Order pickers
Each of the above series has its most applicable occasions and environments, and there are overlapping parts in some functions. For example, counterbalance forklifts, reach forklifts, and overhead stackers can all access the shelf area. Then choose Which model has what kind of benefits to the user in the end?
To give a simple example: Assuming such a warehouse, the goods stored on each pallet are required to be accessible at any time, so they must be placed on both sides of the forklift aisle. On the premise of only considering the plane area, let's take a look at this warehouse Flat utilization of different types of forklifts.
●If the aisle width of the forklift used is roughly equal to the length of the carrier (1500mm), the plane utilization rate can reach 66%;
● If the aisle width of the forklift used is equivalent to twice the length of the carrier (2700mm), the plane utilization rate can reach 50%;
● If the aisle width of the forklift used requires three times the length of the carrier (3500mm), the plane utilization rate can reach 40%;
Obviously, assuming that the floor area of the goods that this warehouse needs to store is 1000m2, then in the first case, 1000/0.66=1515m2 of land is required. This situation is equivalent to the solution of using an overhead stacker or a rail stacker.
In the second case, 1000/0.50=2000m2 of land is required. Equivalent to the use of a reach forklift.
In the third case, 1000/0.40=2500m2 of land is required. Equivalent to the use of counterbalanced forklifts.
Therefore, choosing a suitable forklift can greatly save land and construction investment, which is the most intuitive benefit.
2.Let's take a look at the characteristics of each series of forklifts and their applicable environments
Both manual pallet trucks and electric pallet trucks are used for flat point-to-point transportation. The small and flexible size makes the manual pallet truck suitable for almost any occasion.
However, due to manual operation, it is difficult to transport heavier items of about 2 tons, so it is usually used for frequent short-distance operations of about 15 meters, especially in the loading and unloading areas.
In the future logistics links, manual pallet trucks will also assume the role of connection between various transportation links. Each truck or truck is equipped with a manual pallet truck, which will make loading and unloading operations faster and more convenient. Limited by venue.
When the plane transport distance is about 30 meters, the walking-type electric pallet truck is undoubtedly the best choice. The running speed is controlled by the infinitely variable switch on the handle, and it follows the speed of the operator's walking speed. The safety of operation is guaranteed.
For example, when the distance of the main transportation route is more than 30 meters to about 70 meters, an electric pallet truck with folding pedals can be used, and the driver can stand to drive, and the maximum speed can be increased by nearly 60%. Take Jungheinrich forklift as an example, its new ERE20 It can reach 10 km/h with no load.
The electric stacker is a light-duty indoor lifting and stacking equipment. The body is relatively light, and the arm of the counterweight is lengthened through the support arm at the front of the body to balance the load. Since the fulcrum is outside the center of gravity of the load, the counterweight arm is much larger than the load arm, so a smaller counterweight can lift a larger load.
The use of an electric stacker also has certain limitations. Since the fork and the support arm need to be extended into the bottom of the pallet at the same time, the pallet can be operated, so the double-sided panel cannot be used; also when using the drive-in rack (or the corridor rack) , For the consideration of balance and load bearing, the two sides of the pallet are usually used as the forklift operation surface, and the electric stacker cannot be used at this time.
In conjunction with the shelf design of the electric stacker, beams are often installed on the bottom layer about 100mm above the ground, and the first layer of goods is placed on the bottom beam instead of the ground for forklift positioning.
In fact, we often refer to counterweight forklifts as forklifts, which are also the most widely used and the largest series. Because there is no support arm, a long wheelbase and a large counterweight are required to balance the load, so no matter three-wheel, four-wheel, electric, diesel, the body size and weight are large, requiring a large working space.
At the same time, the fork directly picks up the goods from the front of the front wheel, and there is no requirement for the container; the chassis is high, and the use of rubber tires or pneumatic tires makes it have strong climbing ability and ground adaptability. Therefore, counterbalanced forklifts are generally used for loading and unloading and outdoor transportation.
In the electric counterbalance forklift, it can also be divided into three-wheel and four-wheel, front-wheel drive and rear-wheel drive. Both steering and driving are rear wheels called rear-wheel drive. The advantage is that the cost is lower, and it is easier to locate compared to the front-wheel drive. The drive wheels can slip, and most electric counterbalanced forklifts today use dual-motor front-wheel drive.
Compared with the four-wheel counterbalanced forklift, the three-wheel counterbalanced forklift has a smaller turning radius and is more flexible, and is most suitable for the operation of internal container removal.
There are also two types of diesel and liquefied gas forklifts according to different transmission modes, hydromechanical transmission type and hydrostatic transmission type. Hydromechanical transmission is a more traditional transmission method with low cost, but the transmission efficiency of the torque converter is low, the energy consumption is large, and the later maintenance cost is high.
The hydrostatic transmission is currently the most ideal and most advanced transmission mode for internal combustion forklifts. In outdoor short-distance frequent round-trip transportation, the efficiency of the hydrostatic transmission type internal combustion forklift is significantly improved.
At present, the maximum lifting height of the reach forklift has reached 11.5 meters, the load range is from 1 ton to 2.5 tons, and the multi-reach forklift for accessing long and pipe fittings, indoor and outdoor general-purpose reach forklifts, etc. have been developed. Special purpose product.
The reach forklift combines the advantages of an electric stacker with a support arm and a counterweight forklift without a support arm. At the top, the center of gravity of the load falls on the outside of the fulcrum, which is equivalent to a counterweight forklift; when the gantry is fully retracted, the center of gravity of the load falls on the inside of the fulcrum, which is equivalent to an electric stacker.
The combination of these two performances ensures that the operation flexibility and high load performance are guaranteed, and the volume and self-weight will not increase a lot, saving the working space to the greatest extent.
The most effective operating height of the reach forklift is 6 meters to 8 meters, which is equivalent to a building height of about 10 meters. This height is also the most common building height of stores, distribution centers, logistics centers, and enterprise center warehouses. Within this height range, the operator can see the line of sight, the positioning is fast, and the efficiency is high.
When the operating height is greater than 8 meters, the forklift should be used slowly and carefully when positioning the fork. Usually, auxiliary devices such as a height indicator, a height selector or a camera can be installed.
If the warehouse area is small and the height is high, and a large storage capacity and high transportation efficiency are required, if you do not want to spend a huge investment on automatic warehouses, then the high-bay stacker is the only and best choice. .
The high-level stacker and high-level picking vehicle are usually called VNA (Very Narrow Aisle). The required roadway space is minimal.
The maximum lifting height of VNA series is more than 14 meters, the width of the roadway is usually about 1600mm, and the maximum load is 1.5 tons. It is widely used in the pharmaceutical industry and the electronic and electrical industry.
The overhead stacker can be divided into two types: upper-level and non-climbing. The cockpit is used as the main lift to rise at the same time as the gantry, which is called the upper-level type. The advantage is that it can maintain a horizontal line of sight at any height to ensure the best Visibility to improve operational safety.
At the same time, because the operator can touch the goods at any position on the shelf, it can be used for picking and inventory operations at the same time.
In order to keep the overhead stacker running straight in the aisle, there are two ways: magnetic guide and mechanical guide. Since the magnetic guide must be cut and buried in the center of the roadway, it is easy to damage the floor and difficult to relocate and adjust. Therefore, the most used mechanical guide is currently.
The use of mechanical guidance needs to cooperate with the shelves, install steel rails on both sides of the roadway, guide the roadway through the body guide wheel and other auxiliary devices, and drive in a straight line.
VNA series forklifts are also known as system trucks. There are many coordination and influencing factors to be considered. Therefore, each case needs to be designed separately, and will not be repeated here.
The picking cart series are widely used in distribution centers or third-party logistics warehouses.
Each type of forklift has its corresponding handling capacity, expressed as the number of pallets operated per hour or per day. For different usage environments and different operators, this number is also different, so targeted testing is required.
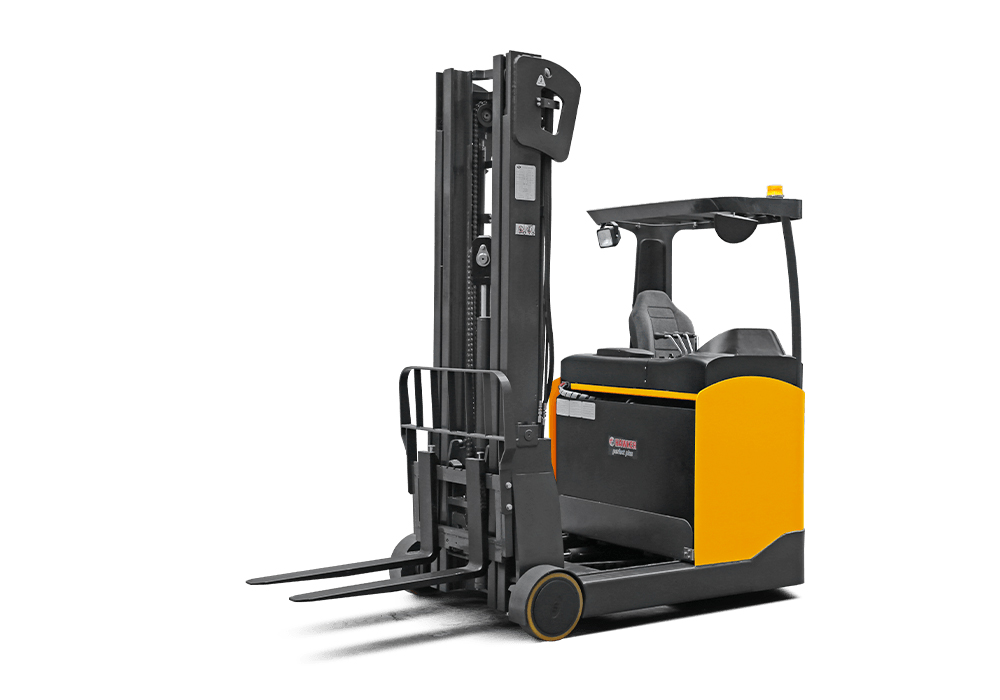
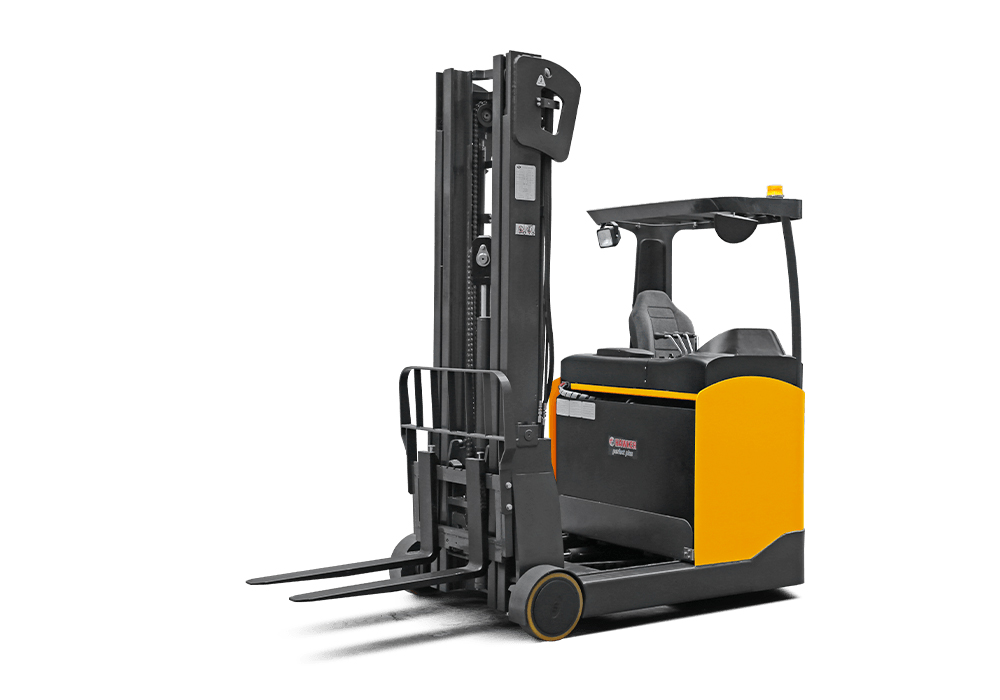
Reach Truck(Sit in)
UN Forklift is one of earliest factories to produce reach truck, double deep reach truck and VNA in China.
UN Forklift is one of earliest factories to produce reach truck, double deep reach truck and VNA in China.
Ergonomic design and high performance supported by innovative technology help UN reach trucks become the perfect solution for various applications in different warehouses.